Porous Carbon Synthesis
Category
Synthesis
Laboratory
Lawrence Livermore National Laboratory (LLNL)
Capability Experts
Theodore F. Baumann ([email protected]), Patrick G. Campbell ([email protected])
Description and Status
LLNL's experimental synthesis capability can provide:
- Synthesis of graphene oxide (GO) and resorcinol formaldehyde (RF) based carbon aerogel materials and composites thereof (including carbon nanotube composites), which result in 3D graphene materials (see Figure 1) with tunable density, crystallinity, pore size, size-distribution, and morphology [1–3]. Complete characterization capabilities, including surface area and pore size (BET/BJH), morphology (SEM/TEM), and mechanical and electrochemical characterization. (Status: 100% on line)
- Advanced manufacturing of porous carbon materials (3D printing). Ability to “print” parts made from porous carbon, control pore size and morphology over several orders of magnitude length scale, with potential to enhance mass transfer/liquid gas flow, etc. (Status: 75% on line, DIW with GO-based inks well established [4], soon-to-publish RF based DIW and PuSL GO inks)
- Conversion of 3D graphene to 3Dh-BN material, including partial conversion to CBN material [5]. (Status: 100% on line for full conversion toh-BN; only partial characterization of CBN material)
- Doping of 3D graphene with B and N (and other) heteroatoms. Methods include incorporation of B, N containing precursor compounds (e.g., N-containing resorcinol analogs), post-synthesis thermal treatment with NH3. (Status: ~50%—synthesis methods developed and limited characterization of N-containing materials performed)
- Infiltration of porous carbon materials with hydrides (e.g., LiBH4). (Status: ~15%, melt infiltration performed on 3D carbon material with large pore size distribution, not characterized)
Figures
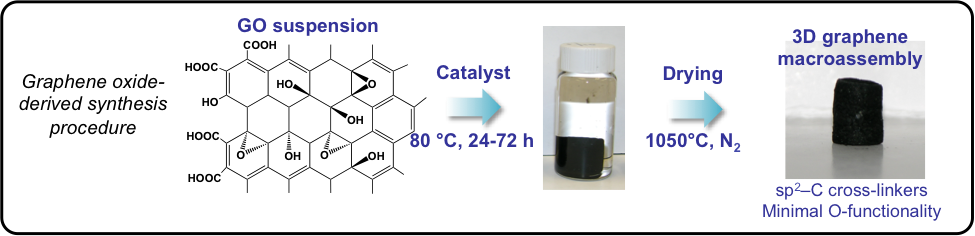
Figure 1. The synthesis procedure of 3D graphene materials derived from graphene oxide (GO).
References
- M. A. Worsley, S. Charnvanichborikarn, E. Montalvo, S. J. Shin, E. D. Tylski, J. P. Lewicki, A. J. Nelson, J. H. Satcher, Jr., J. Biener, T. F. Baumann, S. O. Kucheyev, Adv. Funct. Mater. 24, no. 27 (2014): 4259–4264.
- M. A. Worsley, S. O. Kucheyev, J. D. Kuntz, A. V. Hamza, J. H. Satcher, Jr., T. F. Baumann, Journal of Materials Chemistry 19, no. 21 (2009): 3370–3372.
- M. A. Worsley, T. T. Pham, A. Yan, S. J. Shin, J. R. I. Lee, M. Bagge-Hansen, W. Mickelson, A. Zettl, ACS Nano 8, no. 10 (2014): 11013–11022.
- C. Zhu, T. Y.-J. Han, E. B. Duoss, A. M. Golobic, J. D. Kuntz, C. M. Spadaccini, M. A. Worsley, Nat. Comms. 6 (2015): 6962.
- M. Rousseas, A. P. Goldstein, W. Mickelson, M. A. Worsley, L. Woo, A. Zettl,ACS Nano 7, no. 10 (2013): 8540–8546.